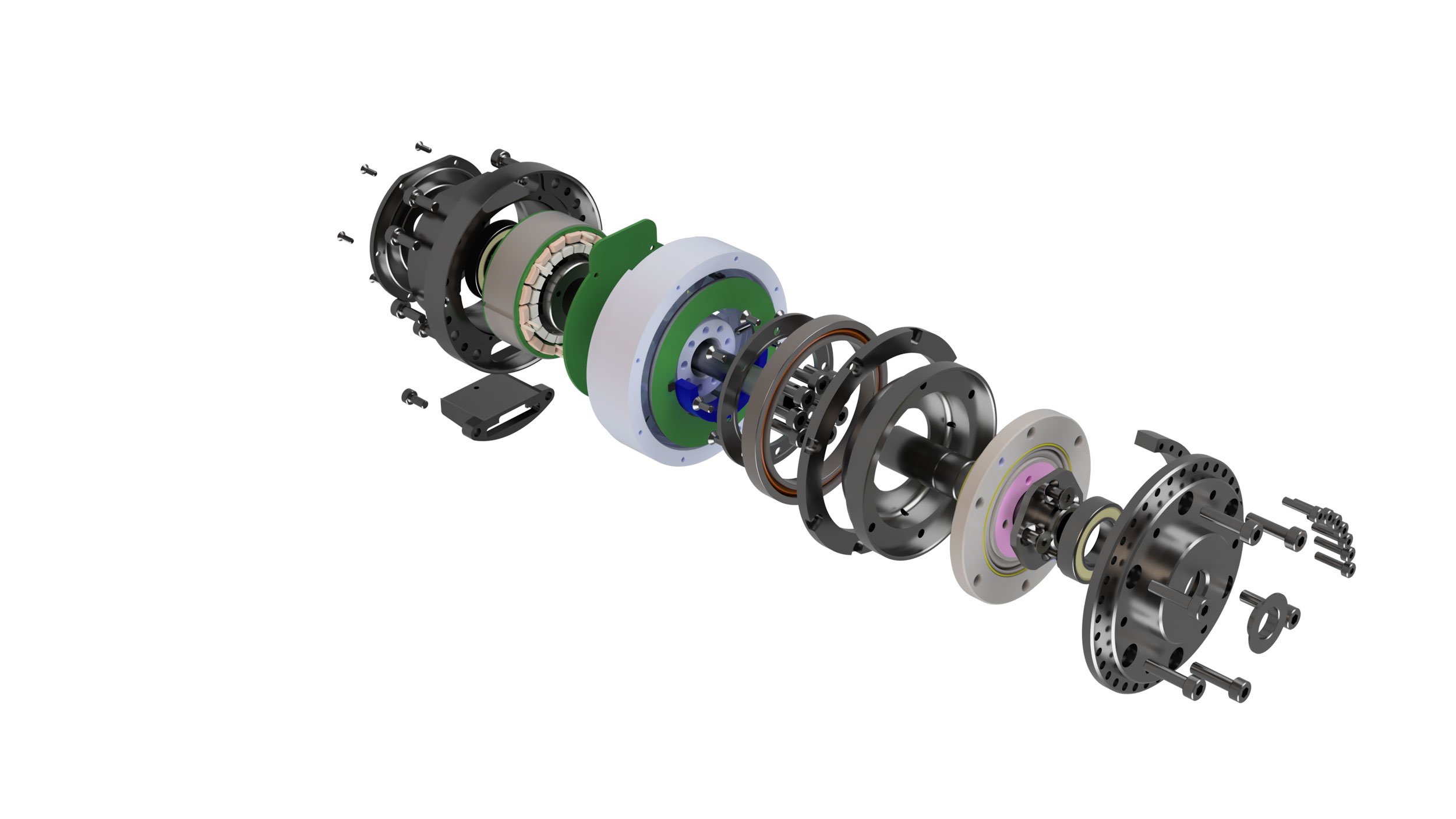
engineering
ARM
Harmonic Drive® based design
Custom motor for best integration
Integrated module electronics
Integrated torque sensor
Capacitive for easy assembly
Motor encoder
High-resolution magnetic encoder
15 bit resolution
Output absolute encoder
MPS magnetic encoder
12 bit resolution
0.4 x 0.4 m workspace in front of robot
Links 0.3 x 0.3 x 0.1 m upper arm x forearm x grip offset
Direct drive large diameter wheels
Kt = .76 Nm/A, 20 A peak
High resolution encoder - IC Haus iC-MU magnetic
36V nominal lithium ion battery, 155 Wh
Basket for items
Camera
Computer - Jetson nano
Approximate footprint 600 x 500 WxL
Large rear caster for navigating outdoors and for sizable obstacles
BASE
Grip
Modular
Software
Motor driver software as available here: github.com/unhuman-io/freebot-controller
Mid-level software, custom 2 kHz real-time loop designed for operation around people: github.com/unhuman-io/freebot-realtime
Gravity compensation
Cartesian impedance control or
Inverse kinematics with joint torque limits
High level software. We provide a scripts and functionality to run robot cameras and use a gamepad to control the robot remotely: github.com/unhuman-io/obot